Quality Assurance Vs. Quality Control Explained: 5 Key Differences
By Marco Franzoni • June 13, 2024
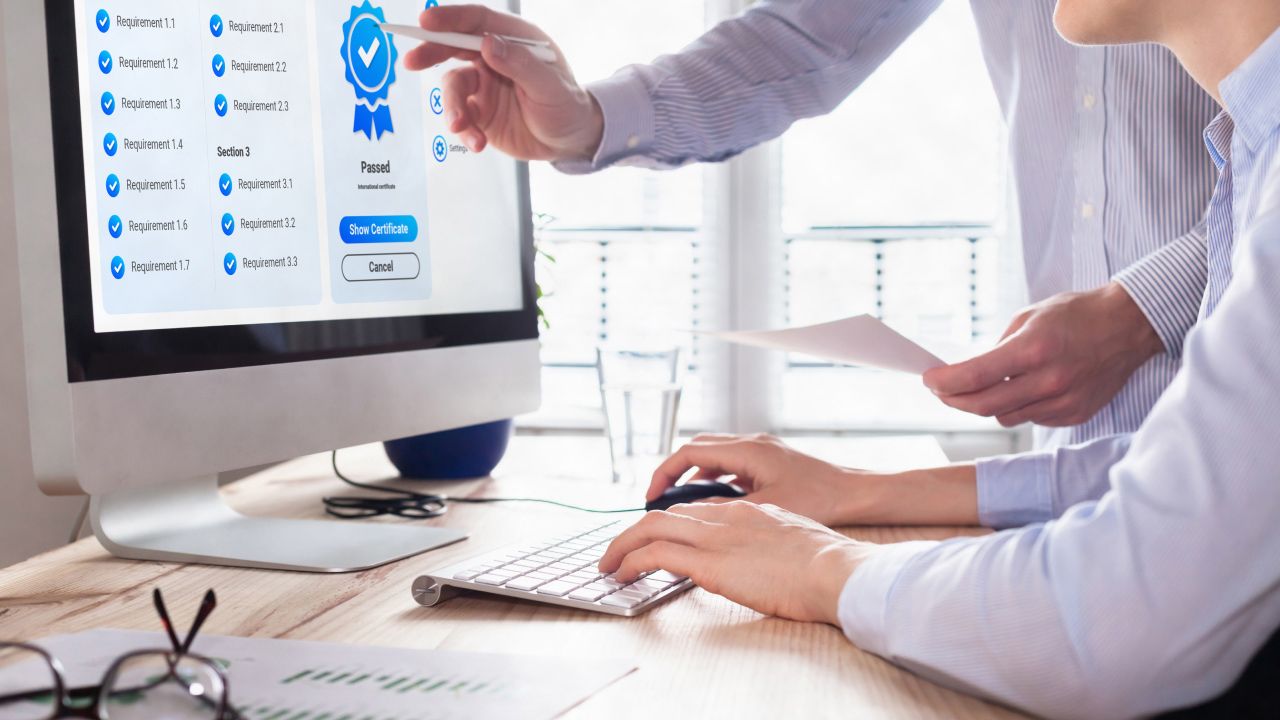
Introduction: Understanding Quality in IT
In today's fast-paced technological landscape, the difference between success and failure often hinges on two critical concepts: Quality Assurance (QA) and Quality Control (QC). These processes not only define the robustness of software and services but also ensure that every aspect of production meets rigorous quality requirements. From enhancing customer loyalty to safeguarding a company’s credibility, QA and QC play pivotal roles in delivering high-quality products that meet specified requirements. This introduction will delve into how these methodologies impact IT operations and why understanding them is crucial for any organization focused on excellence.
What is Quality Assurance?
Defining Quality Assurance in IT Contexts
Quality Assurance (QA) in IT is a proactive process focused on ensuring that software and systems meet predefined quality requirements and work processes. It is integral to maintaining high standards throughout the production process, striving for minimal errors and maximum efficiency.
Quality Assurance Methods
QA employs a variety of methods to verify and enhance the quality of products. This includes statistical process control, rigorous testing procedures, and continuous improvements. A well-implemented QA system not only safeguards a company's credibility but also boosts customer loyalty by delivering reliable and secure services.
What is Quality Control?
Defining Quality Control in IT Contexts
Quality Control (QC) in IT focuses on identifying defects in the final products through rigorous testing and inspection. This reactive process ensures that all software or systems align with the specified requirements and safety standards. By conducting thorough verifications, QC aims to deliver defect-free products, enhancing the efficiency and reliability of the services provided. Through meticulous attention to detail, QC helps maintain a company’s reputation for delivering high-quality products that meet or exceed customer expectations.

Quality Assurance vs. Quality Control: 5 Differences
Process (QA) vs. Product (QC)
Quality Assurance (QA) focuses on preventing defects through the management and improvement of manufacturing and business processes. In contrast, Quality Control (QC) targets the identification of defects in finished products. QA is about processes, while QC is about the product.
Entire Team (QA) vs. Dedicated Personnel (QC)
QA involves the entire team, emphasizing a collaborative approach to maintaining quality throughout the production cycle. On the other hand, QC often relies on a dedicated group of personnel who specifically focus on testing and inspection tasks at the end stages of production.
Quality Assurance Methods vs. Quality Control Tactics
Quality Assurance utilizes methods like process evaluation and improvement, risk management, and statistical process control to ensure quality from the start. Quality Control employs tactics like inspections, testing, and verification to catch errors in finished products.
QA, QC, and Inspection Differences
While QA integrates quality practices throughout the production process, QC conducts targeted inspections at specific stages. Inspection, a core component of QC, is a reactive process designed to identify and fix issues in the final products.
Industry Perspectives on QA and QC
Different industries emphasize various aspects of QA and QC based on their specific needs. For example, in software development, QA might focus on early testing and documentation, whereas in manufacturing, QC could be more about rigorous end-line testing to ensure the safety and durability of physical products.
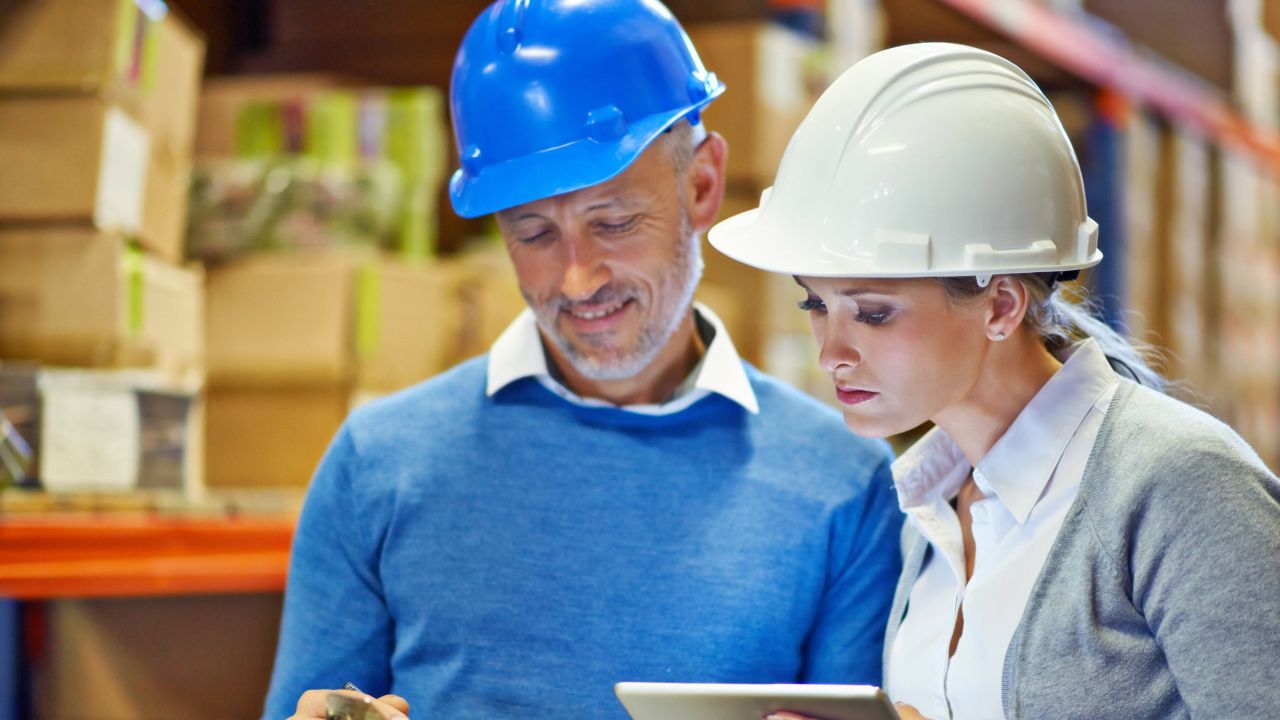
Implementing QA Based on These Examples
Examples of Effective Quality Assurance
Implementing effective Quality Assurance (QA) can significantly enhance efficiency and service quality within any organization. For instance, a software company may integrate automated testing and continuous integration systems to ensure that each code commit meets quality standards before deployment. Similarly, in manufacturing, the use of statistical process control helps monitor the production process in real-time, identifying potential quality deviations before they become costly errors. These examples demonstrate how tailored QA activities can lead to substantial improvements in both product quality and operational efficiency.
History of QA and QC in the IT Industry
History of ISO and QA
The history of Quality Assurance (QA) in the IT industry is closely intertwined with the development of the International Organization for Standardization (ISO). Since its inception, ISO has played a pivotal role in standardizing QA processes across various industries, including IT. The introduction of ISO 9001, a standard that emphasizes quality management systems and statistical process control, marked a significant milestone, setting the global benchmark for quality assurance. This standard has guided countless IT companies in establishing robust QA systems that ensure the production of high-quality software and services.

Conclusion: The Future of QA and QC in IT
Evolving Roles of Quality Assurer Vacancies
As we look to the future, the roles of quality assurance (QA) and quality control (QC) in IT are set to become more integrated and strategic. The demand for quality assurer vacancies is expected to rise, reflecting the growing importance of building customer loyalty and maintaining a company's credibility through high-quality services. Innovations in QA and QC processes will continue to shape how companies implement these crucial functions, ensuring that quality remains at the forefront of technological advancements and business practices.