Maximizing Efficiency And Minimizing Rework With Six Sigma First Time Yield
By Marco Franzoni • August 23, 2024
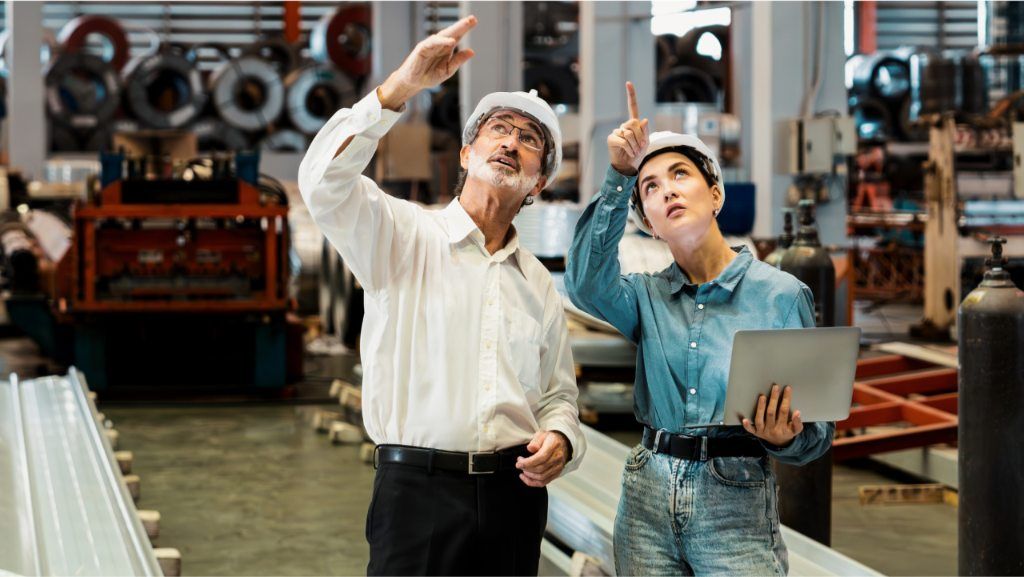
Introduction: Maximizing Efficiency with Six Sigma First Time Yield
In today's rapidly evolving manufacturing world, efficiency isn't just a goal—it's a critical necessity. Factory managers across the globe are constantly seeking ways to optimize production, reduce waste, and ensure the highest quality in their output. But achieving this level of excellence requires more than just good intentions; it requires a strategic approach rooted in proven methodologies.
This is where Six Sigma steps in, offering a structured, data-driven framework for improving manufacturing processes. For factory managers, understanding and implementing Six Sigma principles can be the difference between success and failure in a highly competitive market.
One of the most important metrics within the Six Sigma methodology is First Time Yield (FTY). FTY focuses on the number of units that pass through a process without requiring any rework or corrections. By calculating and improving FTY, factories can significantly reduce rework, boost efficiency, and deliver higher quality products to their customers.
Definition of First Time Yield (FTY)
What is FTY?
First Time Yield (FTY) is a critical metric in the manufacturing industry, representing the percentage of products that pass through a production process without needing any rework or corrections. Essentially, it measures the effectiveness of a process by focusing on the quality of output at the first attempt. FTY is especially important for factory managers who aim to optimize production and reduce waste, as it directly correlates with the overall efficiency and quality of a manufacturing process.
Importance of Accurate FTY Calculation in Manufacturing Processes
Accurately calculating FTY is crucial for identifying inefficiencies and areas for improvement within a factory's operations. When FTY is measured correctly, it provides factory managers with valuable insights into the effectiveness of their processes, allowing them to make informed decisions about where to focus their efforts to enhance production quality. Moreover, a high FTY often indicates that many processes are running smoothly, which leads to reduced costs, higher customer satisfaction, and a stronger competitive position in the marketplace.
Importance of FTY in Six Sigma
Role of FTY in Six Sigma Methodology
In the realm of Six Sigma, First Time Yield (FTY) serves as a vital metric that gauges the quality and efficiency of manufacturing processes. Six Sigma methodologies are centered on reducing defects and enhancing process consistency, and FTY directly aligns with these goals. By calculating the total number of units that pass through a process without needing rework, FTY provides factory managers with clear insights into where improvements can be made. Whether you're operating in a leading city or a more remote location, understanding and implementing FTY is crucial for maintaining high standards in manufacturing and production.
How FTY Contributes to Overall Process Efficiency
A high FTY is a strong indicator that your manufacturing processes are optimized, with several features performing at their best. This not only reduces waste but also streamlines production and enhances customer satisfaction. By focusing on FTY, factory managers can ensure that every feature of the process is contributing positively, leading to a more efficient operation overall. Moreover, consistently achieving high FTY can be a key factor in the continuous development and improvement of your manufacturing systems, making it an essential component of any Six Sigma strategy.
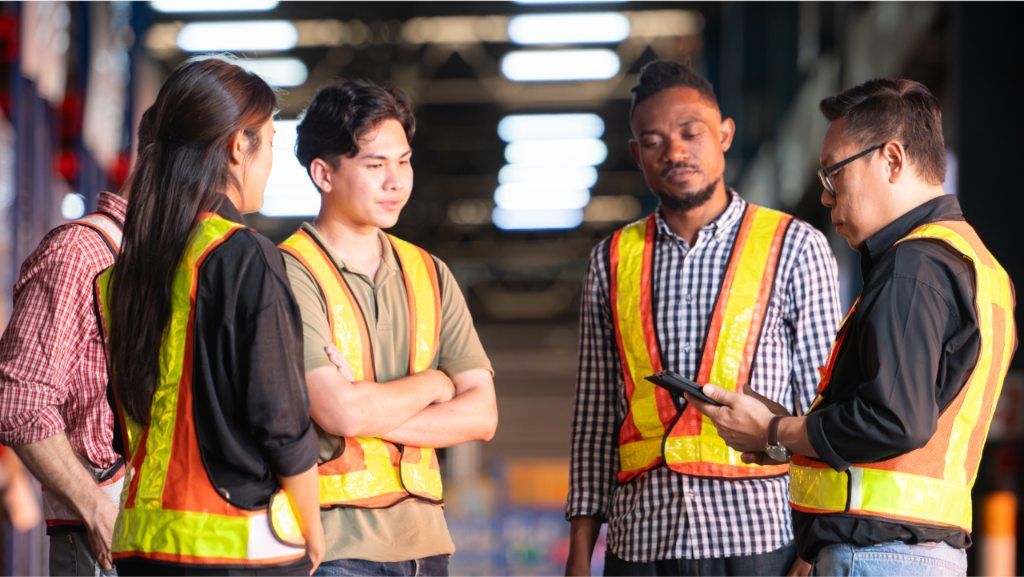
Identifying Process Improvement Opportunities with FTY
Using FTY to Spot Inefficiencies in Manufacturing Processes
First Time Yield (FTY) is a powerful tool that factory managers can use to identify and address inefficiencies within their manufacturing processes. By carefully calculating FTY, you can pinpoint specific areas where processes may be underperforming, leading to a lower yield. For example, if a particular step in the production line consistently results in defects, this would be reflected in a lower FTY, signaling a need for process improvement. By focusing on these areas, managers can take targeted actions to reduce waste, improve quality, and enhance overall production efficiency.
Case Studies or Examples of FTY-Driven Improvements
There are numerous examples of how FTY has been successfully employed to drive significant improvements in factories around the world. In one case, a factory in London was able to increase its FTY by 20% by addressing a critical bottleneck in its assembly line. This improvement not only boosted production efficiency but also reduced costs and increased customer satisfaction. Another example comes from a leading city in the U.S., where FTY was used to identify and correct a recurring issue in the building materials production process, resulting in a dramatic reduction in rework and scrap. These case studies highlight the importance of FTY in achieving tangible improvements and demonstrate its effectiveness as a metric for continuous process optimization.
First Time Yield vs. Rolled Throughput Yield (RTY)
Definition and Comparison of FTY and RTY
First Time Yield (FTY) and Rolled Throughput Yield (RTY) are essential metrics that help factory managers measure the effectiveness of their production processes. FTY is concerned with the total number of units that pass through a specific process without needing rework, giving a precise snapshot of that particular step's efficiency. In contrast, RTY looks at the entire range of processes involved in production, calculating the probability that a unit will pass through all steps without defects. While FTY can be seen as a characteristic measure of specific stages, RTY represents the overall quality of the production line.
When to Use FTY vs. RTY in Process Evaluation
The decision to use FTY or RTY depends on the specific goals and characteristics of the manufacturing process. Factory managers might prefer FTY when focusing on improving individual parts of the process, such as in building feature-rich products where certain steps are more prone to errors. On the other hand, RTY is more beneficial when the focus is on the total number of units successfully passing through the entire production cycle, which can be particularly important in leading city factories where large-scale production and overall efficiency are key. Both metrics are invaluable in helping managers calculate, measure, and ultimately enhance the quality and efficiency of their manufacturing operations.
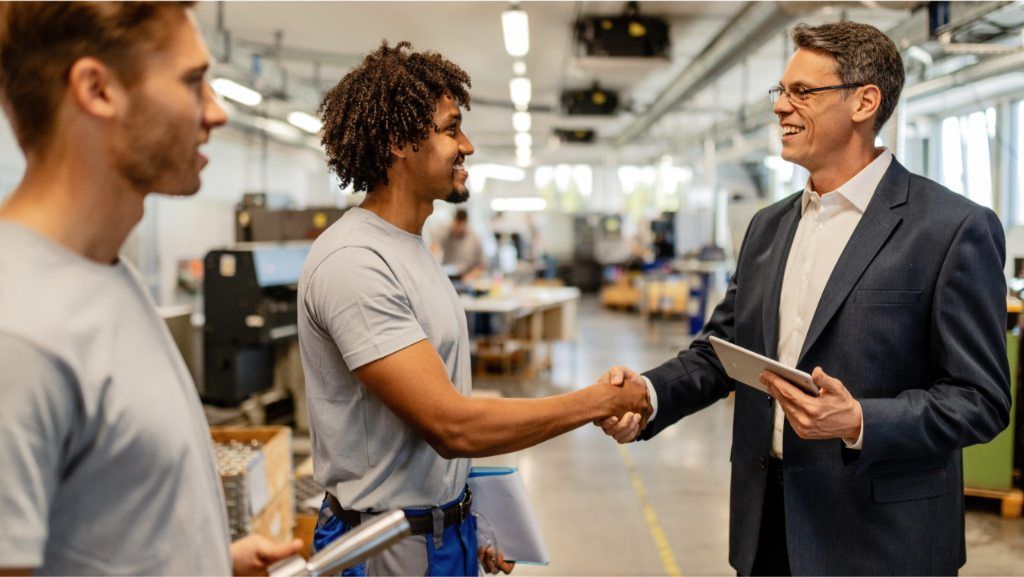
Practical Steps to Improve First Time Yield
Strategies to Enhance FTY in Your Factory
Improving First Time Yield (FTY) is crucial for factory managers aiming to boost production efficiency and reduce waste. One effective strategy is to focus on optimizing the most critical features of your production process. This could involve identifying and addressing the specific characteristics of each step that are prone to errors. For example, ensuring that the materials used are of consistent quality can significantly impact FTY. Additionally, investing in employee skills training and workshops can help to minimize human errors, leading to a smoother production flow. Regularly reviewing and updating your production processes, especially in leading factories in major cities like London, can also provide new insights and opportunities for improvement.
Role of Continuous Monitoring and Adjustments
Continuous monitoring is essential for maintaining and improving FTY over time. By consistently tracking FTY metrics, factory managers can quickly identify when and where problems arise. This allows for timely interventions and adjustments to the processes before they escalate into larger issues. For example, using real-time data analytics to monitor production performance can help managers calculate and measure the impact of changes in the process, ensuring that adjustments lead to tangible improvements. Implementing a robust plan for continuous monitoring and making regular, data-driven adjustments is key to sustaining high FTY and maintaining optimal production efficiency.
Benefits of High First Time Yield in Manufacturing
Reduced Rework and Waste
Achieving a high First Time Yield (FTY) is a crucial objective for factory managers who aim to streamline operations and enhance overall efficiency. One of the most immediate and tangible benefits of a high FTY is the significant reduction in rework and waste. When products pass yield requirements the first time, it eliminates the need for corrections or adjustments, which can be time-consuming and costly. In many cases, rework involves not only additional labor but also the use of extra materials, both of which contribute to increased production costs. By focusing on improving FTY, factory managers can effectively remove these inefficiencies from their processes.
For example, consider a scenario where a factory produces a batch of components for a feature film production. If these components do not meet the required quality standards on the first pass, the factory must allocate additional resources to correct the defects. This not only delays the delivery of the components but also increases production costs. However, if the factory achieves a high FTY, the components would meet quality standards on the first attempt, saving time and reducing waste. This efficiency is particularly important in industries with tight deadlines and high production volumes, where any delay can have significant financial implications.
Improved Product Quality and Customer Satisfaction
High FTY is also directly linked to improved product quality. When products are manufactured correctly on the first attempt, it ensures consistency and adherence to quality standards, which is critical for maintaining customer satisfaction. Customers expect products that meet their expectations in terms of performance, durability, and reliability. When a factory consistently delivers high-quality products, it not only satisfies existing customers but also builds a strong reputation in the market, attracting new customers and increasing market share.
This is akin to a feature film production where the audience expects a seamless viewing experience. Just as a film must be meticulously edited to ensure that every scene meets the director’s vision, products must be carefully manufactured to meet customer specifications. A high FTY means fewer defects and higher consistency, which directly translates into better customer experiences. Factory managers who focus on improving FTY are, in essence, ensuring that their "audience" — the customers — are delighted with the final product.
Moreover, the ripple effects of high FTY extend beyond the factory floor. As customer satisfaction improves, so does customer loyalty, leading to repeat business and positive word-of-mouth. In today’s competitive market, where customer reviews and opinions can significantly influence purchasing decisions, maintaining a high FTY is a strategic advantage that cannot be overlooked.
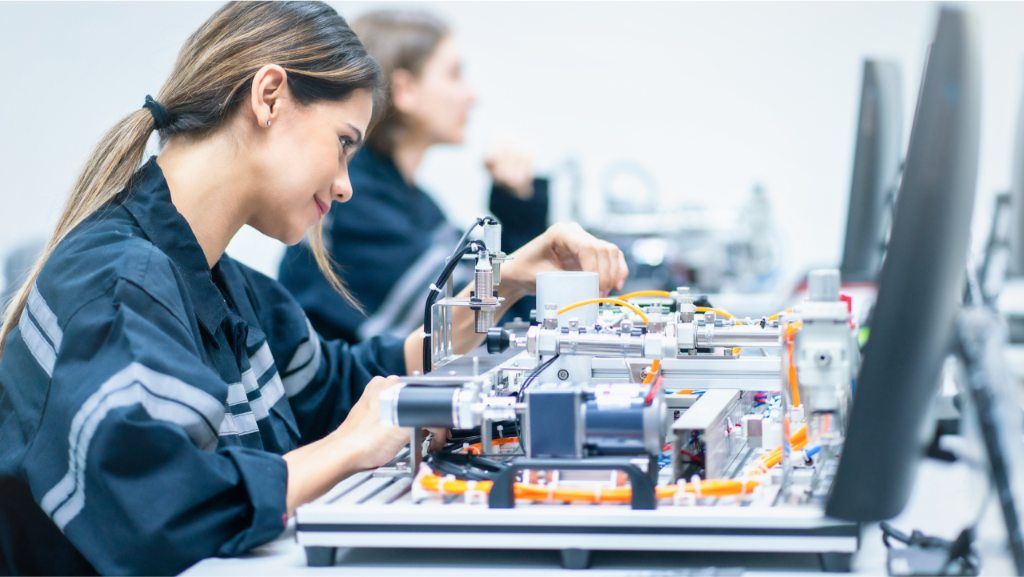
Cost Savings and Profitability
In addition to reducing waste and enhancing product quality, high FTY also contributes to substantial cost savings and increased profitability. Factories that consistently achieve high FTY can produce more with the same resources, leading to higher output and lower costs per unit. This efficiency is particularly important in industries where margins are tight and competition is fierce.
For instance, consider a factory that produces components for a feature film set. If the factory can produce these components with a high FTY, it can meet tight production schedules without incurring additional costs for rework or delays. This efficiency not only saves money but also ensures that the factory can take on more projects, increasing its overall profitability.
Moreover, the financial benefits of high FTY extend beyond the immediate cost savings. By reducing waste and improving efficiency, factories can allocate resources more effectively, investing in new technologies, training, and process improvements that further enhance productivity. This creates a virtuous cycle where high FTY leads to cost savings, which in turn funds further improvements, leading to even higher FTY and greater profitability.
Long-Term Strategic Benefits
Finally, the long-term strategic benefits of high FTY should not be underestimated. In a world where consumer expectations are constantly evolving, and competition is increasingly global, maintaining a high FTY is essential for staying ahead of the curve. Factory managers who prioritize FTY are not just improving their current operations; they are also positioning their factories for future success.
By consistently delivering high-quality products on time and at a competitive cost, these factories build strong relationships with their customers and establish themselves as reliable partners in the supply chain. This reliability is a key differentiator in a crowded market and can be the deciding factor in securing new contracts and expanding into new markets.
Moreover, the focus on FTY fosters a culture of continuous improvement within the factory. Employees become more engaged in identifying and solving problems, leading to a more dynamic and innovative work environment. This culture of excellence not only improves FTY but also enhances overall organizational performance, making the factory more resilient and adaptable in the face of changing market conditions.
Conclusion: Leveraging FTY for Optimal Efficiency
Throughout this post, we’ve explored the critical role that First Time Yield (FTY) plays in enhancing efficiency and reducing rework in manufacturing. By understanding and implementing FTY, factory managers can drive significant improvements in their processes, leading to better product quality, cost savings, and increased profitability. The Six Sigma methodology, with FTY as a core metric, offers a clear pathway to achieving these goals.
As factory managers look to the future, embracing FTY in their operational strategies will be essential for staying competitive in an ever-evolving industry. The focus on continuous improvement, guided by FTY, not only benefits the current state of manufacturing but also sets the stage for future advancements in efficiency and productivity.
By prioritizing FTY, factory managers can ensure that their processes are optimized, their teams are engaged, and their customers are satisfied, paving the way for sustained success in the manufacturing sector.