What Is A Continuous Improvement Process? Tips For IT Leaders
By Marco Franzoni • October 10, 2024

Introduction: What Is A Continuous Improvement Process?
In today’s fast-paced and competitive business environment, companies that stand still are often left behind. Organizations that thrive are those that constantly seek ways to enhance their operations, refine processes, and adapt to changing market conditions. This is where the continuous improvement process comes into play. It's not just a business strategy; it's a mindset and a culture of ongoing improvement that drives incremental improvements and significant advancements over time.
For IT leaders, adopting a continuous improvement model is essential to stay ahead in a rapidly evolving technological landscape. From enhancing existing processes to implementing small improvements that yield substantial results, continuous improvement ensures that companies remain agile and responsive. This approach emphasizes not only boosting efficiency but also fostering employee engagement and customer satisfaction by identifying opportunities for better workflows and eliminating waste.
Understanding and applying a continuous improvement process allows IT leaders to streamline operations, adapt to shifting market conditions, and meet growing customer needs. By embedding continuous improvement efforts into the company culture, organizations can achieve operational excellence and sustain success.
Overview of continuous improvement in business
- Continuous improvement focuses on ongoing refinement of business processes, aiming for incremental improvements rather than large-scale overhauls.
- This ongoing effort leads to cost reduction, improved quality, and increased efficiency.
Importance of continuous improvement for IT leaders
- In the IT sector, where process changes are frequent, a continuous improvement program helps manage the complexity and deliver efficient workflows.
- By adopting process improvement methods like lean methodologies or the PDCA cycle, IT leaders can improve processes, streamline operations, and reduce defects, ultimately fostering customer focus and satisfaction.
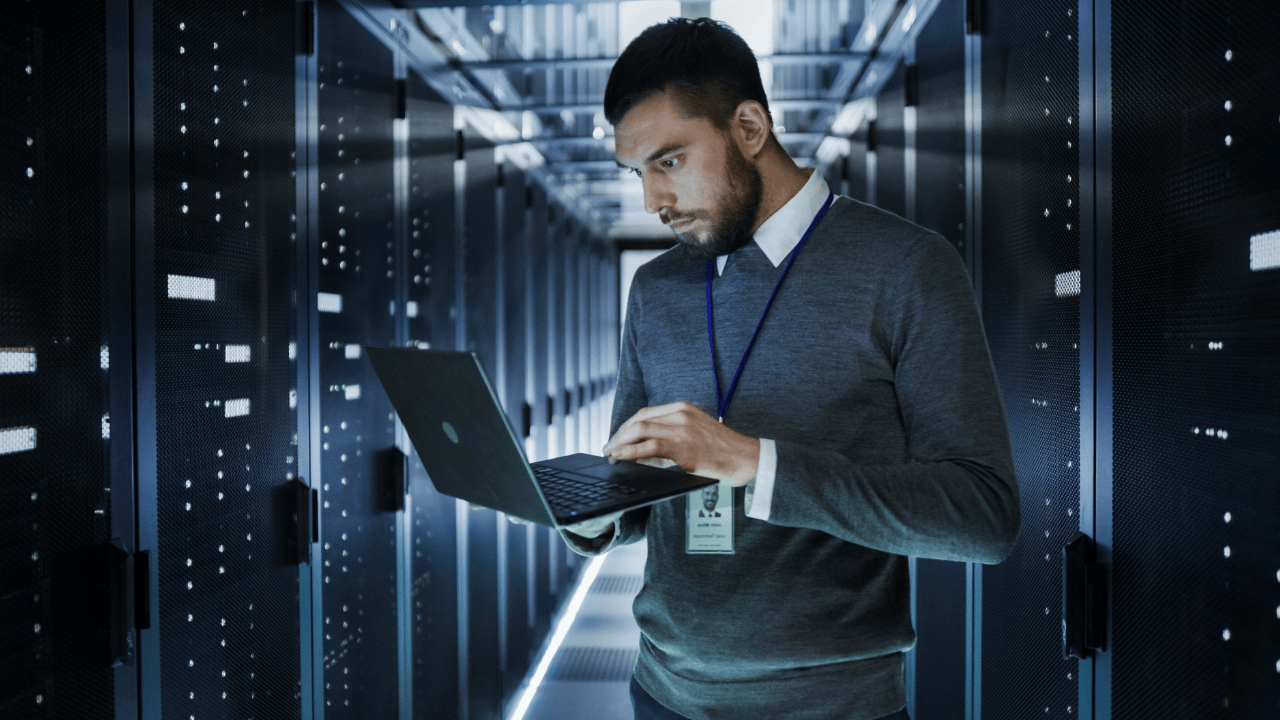
Why Use a Continuous Improvement Process?
In an era of constant change and competitive pressure, businesses must continuously adapt to survive and thrive. Implementing a continuous improvement process provides a structured way to improve processes and enhance overall performance. It enables organizations to make incremental improvements over time, leading to significant improvements in efficiency, quality, and customer satisfaction.
Benefits of continuous improvement for business outcomes
A well-executed continuous improvement model has far-reaching benefits for business outcomes. By focusing on ongoing improvement and consistently refining existing processes, organizations can realize substantial cost savings and operational excellence. Whether it's through reducing waste, eliminating defects, or streamlining workflows, a continuous improvement program enhances the company's ability to meet customer needs while keeping costs under control. This results in a continuous improvement cycle where every process is subject to review, adaptation, and improvement.
Enhanced adaptability in fast-changing industries
Industries, particularly technology, evolve at breakneck speed. Businesses that rely on outdated methods risk being left behind. A continuous improvement process ensures that companies can adapt quickly to changes in market conditions, technological advancements, and customer complaints. This ongoing process allows for process improvement techniques to be applied systematically, ensuring increased efficiency and quality control in every aspect of the business.
The Roles of Continuous Improvement and Process Improvement in Business
Both continuous improvement and process improvement play integral roles in driving long-term business success. While the two concepts are closely related, they serve distinct purposes that together create a culture of ongoing improvement.
Distinction between continuous improvement and process improvement
Continuous improvement refers to the ongoing, incremental approach to refining processes over time, often through a continuous improvement model like Kaizen or Lean methodologies. It’s an ongoing process that encourages businesses to always seek better ways of doing things, making small improvements that accumulate into significant improvements.
On the other hand, process improvement focuses on identifying specific issues within existing processes and implementing structured methods to resolve them. Utilizing various process improvement techniques like value stream mapping or root cause analysis, businesses can target inefficiencies, streamline workflows, and eliminate waste.
Why both are crucial for long-term success
By combining the continual improvement mindset of continuous improvement with the structured, issue-targeting nature of process improvement, businesses can sustain operational excellence and adapt to changing market conditions. The two approaches ensure not only incremental improvements in day-to-day operations but also targeted breakthroughs in business processes that support larger organizational goals.
Together, they foster a culture of innovation and adaptability, enabling businesses to maintain competitiveness in the face of shifting demands and customer needs.
Common Continuous Improvement Process Methods
A variety of methodologies support the concept of continuous improvement, each tailored to ensure incremental improvement and successful implementations. Among the most effective methods are Lean, Six Sigma, and the PDCA cycle. These frameworks allow businesses to streamline processes and consistently identify and implement small improvements that lead to significant results over time.
Overview of key methods (Lean, Six Sigma, PDCA)
- Lean Methodology: Developed from the Toyota Production System, Lean focuses on reducing defects and eliminating waste while maximizing value. Its tools, like value stream mapping and the Kanban method, help businesses enhance efficiency by continuously refining current processes.
- Six Sigma: This data-driven methodology aims to improve quality by reducing variability in business processes. Six Sigma’s structured DMAIC framework ensures that businesses can identify key principles, make new process changes, and track outcomes to refine their methods over time.
- Plan-Do-Check-Act (PDCA) Cycle: As one of the most widely used tools in continuous process improvement, the PDCA cycle encourages organizations to test improvements in a controlled environment, assess the results, and refine them iteratively. This structured approach mirrors the scientific method in a business setting.
How these methods are applied in IT
In IT, these methodologies help streamline processes like software development, network management, and IT service delivery. Lean tools identify bottlenecks, while Six Sigma reduces coding errors and service interruptions. The PDCA cycle facilitates regular testing and refinement of IT solutions, ensuring new processes align with company goals. By fostering a continuous improvement culture, IT leaders can drive employee involvement, ensuring both operational excellence and continuous improvement in quality across the board.
Six Sigma Methodology and the DMAIC Process
The Six Sigma methodology is a powerful tool for businesses looking to enhance their continuous improvement efforts. At its core, Six Sigma focuses on process optimization through the reduction of defects and variability, leading to more efficient and reliable processes. This approach allows organizations to streamline processes and achieve incremental improvements that lead to significant gains in both performance and quality control.

How Six Sigma contributes to process optimization
Six Sigma employs a structured approach to apply continuous process improvement by identifying and eliminating sources of inefficiency and waste. It combines statistical analysis with practical tools to help organizations refine current processes and achieve improved quality. The goal is to drive successful implementations that not only reduce costs but also increase customer satisfaction and operational excellence.
Key features of the DMAIC process
At the heart of Six Sigma is the DMAIC process—a five-step methodology designed to guide businesses through problem-solving and process improvement:
- Define: Identify the issue and set clear objectives.
- Measure: Collect data to understand the scope of the problem.
- Analyze: Use statistical tools to determine the root causes.
- Improve: Implement solutions to address the issues, making incremental improvements.
- Control: Establish controls to maintain the improvements and ensure long-term success.
The DMAIC process enables organizations to identify key features of inefficiency, improve new processes, and ensure that small improvements accumulate into larger, more impactful outcomes. This methodology aligns with lean principles and can be applied in various industries, including IT, to achieve continuous process improvement and maintain a continuous improvement culture.
The Plan-Do-Check-Act Principle (PDCA)
The Plan-Do-Check-Act (PDCA) principle is a foundational tool in continuous improvement and total quality management. It provides a structured approach for refining current processes and achieving incremental improvement through a cyclical method. PDCA fosters a continuous improvement culture by encouraging businesses to continually assess and adjust their methods, driving both small improvements and long-term change.
Steps of PDCA and their application in IT
The PDCA cycle consists of four phases:
- Plan: Identify opportunities for improvement and develop a plan to address them.
- Do: Implement the plan on a small scale to test its effectiveness.
- Check: Assess the results and compare them to the expected outcomes, identifying any issues or areas for further improvement.
- Act: If successful, scale the implementation, integrating it into current processes and making it part of the organization's routine operations.
In IT, PDCA is especially useful for improving software development, network management, and service delivery. This cycle allows IT teams to continuously refine processes, address issues, and implement new strategies, ensuring successful implementations while reducing defects and improving overall efficiency.
Comparison with other methodologies
While methodologies like Lean and Six Sigma emphasize eliminating waste and reducing variability, PDCA offers a more flexible, iterative approach that encourages regular feedback and adaptation. Unlike the rigid structures of other methods, PDCA focuses on continuous, small-scale improvements, making it highly adaptable to various business processes and new processes across industries. This flexibility makes PDCA one of the most widely used tools for organizations pursuing continuous process improvement and quality control.
Kaizen and Kata: The Power of Incremental Improvements
The Japanese philosophy of Kaizen has played a pivotal role in shaping the modern approach to continuous improvement. Rooted in the belief that small, consistent changes can lead to significant long-term results, Kaizen is all about making incremental improvements in business processes. By focusing on gradual, continuous changes rather than sweeping overhauls, Kaizen has contributed to Japan’s competitive success and inspired many organizations around the world to adopt a similar mindset.
The philosophy of Kaizen and its long-term impact
Kaizen emphasizes a culture of ongoing improvement, where every employee is involved in identifying opportunities for enhancing processes. This philosophy not only improves operational efficiency but also fosters a sense of ownership and employee involvement. Over time, the basic principles of Kaizen help businesses achieve better performance, lower costs, and higher quality control. It’s a gradual but powerful method for streamlining processes, as it focuses on small, manageable changes that accumulate into substantial improvements.

Introduction to Kata: structured improvement routines
Kata, a method derived from Kaizen, offers a more structured approach to continuous improvement efforts. It involves creating standardized routines for problem-solving and process improvement. Kata routines are designed to guide employees in developing a mindset focused on continuous process improvement. By practicing Kata regularly, teams can make small improvements and adjustments that lead to improving processes on a larger scale.
Both Kaizen and Kata have become essential tools for successful companies worldwide, allowing them to maintain flexibility, enhance efficiency, and continually adapt to changes in the market while ensuring improving quality over time.
Continuous Improvement Tools and Methodologies
To effectively implement a continuous improvement process, organizations rely on a range of tools and methodologies that streamline efforts and enhance efficiency. These tools allow businesses to make incremental improvements and adapt to shifting market demands, ensuring long-term success. From BPM software to structured techniques like PDSA and PARS, these methodologies provide a clear framework for improving processes and driving innovation.
Common tools (PDSA, BPM software)
One of the most commonly used tools in continuous process improvement is the PDSA cycle (Plan-Do-Study-Act), which offers a simple yet effective method for testing and refining improvements. This cycle encourages teams to plan, test, and review changes on a small scale before wider implementation, ensuring improving quality and minimizing risk.
Additionally, Business Process Management (BPM) software helps businesses automate and streamline workflows. This tool enables organizations to identify inefficiencies, streamline processes, and measure progress more effectively, allowing for continuous refinement and better alignment with organizational goals.
PARS: What Are They & Why You Should Use Them
PARS (Problem, Action, Result, and Solution) is another valuable tool in the world of continuous improvement. It provides a structured approach to problem-solving by breaking down each improvement effort into clear steps. Successful companies use PARS to guide employees through the process of identifying issues, taking action, and ensuring that the changes lead to measurable improvements.
By utilizing these tools and methodologies, many organizations are able to scale their efforts, make significant improvements, and maintain their competitive edge. The consistent application of these techniques helps businesses operate at a larger scale, achieve improving quality, and contribute to Japan's competitive success in global markets.
Small Changes, Big Results: How Incremental Improvements Add Up
The essence of continuous improvement lies in making small, incremental changes that lead to significant results over time. In industries like IT, where rapid adaptation is crucial, even minor adjustments can have a profound impact on efficiency, quality, and performance. These small improvements, when applied consistently, contribute to streamlining processes and achieving larger organizational goals.
Examples of small, impactful changes in IT
In IT, continuous process improvement often involves optimizing code, refining software testing methods, or automating repetitive tasks. For example, a small tweak in server management could drastically reduce downtime, while incremental changes in coding standards might prevent critical bugs, thereby improving quality and system reliability.
Case studies of long-term success from small changes
Successful companies across the globe, including those that have contributed to Japan’s competitive success, have adopted the principle of making small improvements for long-term gains. By focusing on basic principles of improving processes, organizations can scale these changes and see results on a larger scale. For instance, Toyota’s gradual adjustments to its manufacturing process through Kaizen led to significant efficiency gains and cost reductions, positioning it as a global leader in operational excellence.
In IT and beyond, many organizations have proven that continuous, incremental improvements are the key to sustained growth and success.
Enhanced Employee Engagement through Continuous Improvement
One of the core principles of any successful continuous improvement program is the active involvement of employees at every level. Engaging employees not only improves processes but also boosts morale by giving individuals a sense of ownership and responsibility in the organization’s success. When employees feel valued and are directly involved in continuous improvement efforts, they are more motivated and committed to achieving the company’s goals.
How involving employees improves processes and morale
Encouraging employee engagement in the continuous improvement process leads to more innovative solutions. Employees who are directly involved in daily operations are often the first to spot inefficiencies and suggest practical changes. This hands-on participation not only drives process improvement but also increases job satisfaction, as employees see the tangible impact of their contributions. Over time, this creates a culture where continuous improvement becomes second nature.

The role of feedback loops in continuous improvement
Feedback loops play a crucial role in sustaining continuous improvement. Regularly soliciting and acting on employee feedback helps organizations fine-tune their improvement process, ensuring that small adjustments lead to better outcomes. These feedback loops create an environment of open communication, fostering employee engagement and making continuous improvement a collaborative effort that benefits the entire organization.
Continuous Improvement Limitations and Overcoming Obstacles
While the continuous improvement process offers many benefits, it is not without its challenges. Implementing a successful continuous improvement program requires commitment, persistence, and the ability to adapt. Organizations often face obstacles such as resistance to change, lack of resources, or difficulty in maintaining momentum. However, understanding these limitations and employing effective strategies can help overcome them and ensure long-term success.
Common challenges with implementing continuous improvement
One of the most common challenges is employee resistance. Without proper employee engagement, teams may feel overwhelmed by constant changes or fear their roles may become redundant as processes evolve. Additionally, organizations may struggle with limited resources or time constraints, making it difficult to dedicate the necessary attention to the continuous improvement process. Another issue is the failure to maintain focus, where organizations initiate improvement efforts but lose momentum over time.
Strategies to overcome obstacles and stay on track
To combat these challenges, organizations must adhere to the core principles of continuous improvement. Ensuring strong employee engagement from the start is essential. Encouraging participation through regular feedback loops and transparent communication can alleviate resistance and foster a collaborative atmosphere. Additionally, it’s important to start with small, manageable goals and incremental improvements. This keeps momentum steady and builds confidence in the continuous improvement program. Organizations should also allocate dedicated resources and time to the process improvement efforts, reinforcing the importance of long-term commitment.
By recognizing these obstacles and actively working to overcome them, organizations can stay on track and continue to reap the benefits of their continuous improvement efforts.
Conclusion: Continuous Improvement as a Strategy for IT Leaders
As we’ve explored throughout this post, adopting a continuous improvement process is essential for IT leaders aiming to achieve operational excellence. By consistently applying continuous process improvement methods such as Lean, Six Sigma, and PDCA, organizations can make incremental improvements that lead to increased efficiency, cost savings, and long-term success.
The improvement cycle is ongoing, and its benefits grow over time, fostering a culture of innovation and adaptability. IT leaders are encouraged to embrace these practices, embedding them into their teams' daily operations. This not only drives continuous improvement efforts but also positions organizations to remain competitive and responsive to evolving market demands.
By implementing small, consistent changes, IT leaders can unlock new levels of productivity, efficiency, and excellence.